CHP
This page of the tool contains calculations for both the hot water and steam CHP options. As these options are effectively extensions of the electricity generation options, it is assumed the income calculated on the Electricity Generation page also applies here. However additional benefits are achieved through the production of heat.
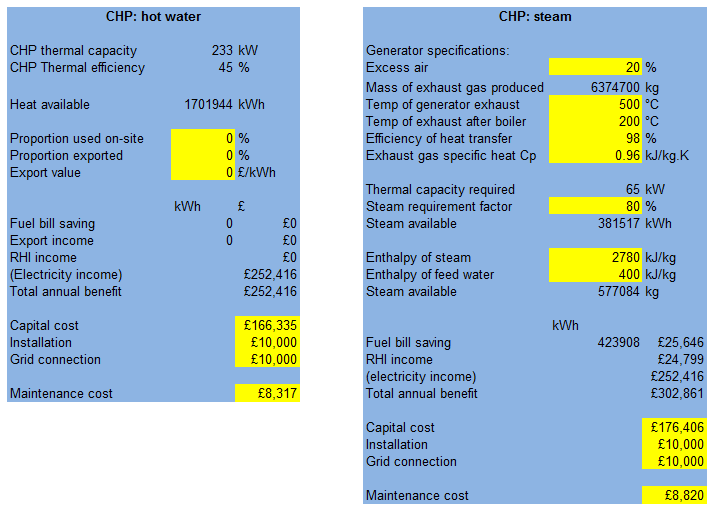
CHP: Hot Water
Packaged CHP units producing hot water at 90°C are readily available. However in general distilleries have little demand for low grade heat. This option may only be economically attractive if heat can be exported, or if the heat demand of the AD system is large. Key cells are:
- Heat Available: This is the amount of heat generated, minus the heat demand of the AD system.
- Proportion Used On-site: Ss distilleries typically have no demand for low grade heat, as a default the tool assumes that none of the hot water produced is used on site. However if this is changed by the user, the tool calculates a fuel bill saving based on cost of generating heat using the distillery’s current boiler.
- Proportion Exported: Whether or not heat can be exported depends very much on a distillery’s location. Again as a default the tool assumes that no heat is exported.
- Export Value: There is not yet an established market for heat in the UK, and so a typical price is not available. The export value must therefore be input by the user.
RHI support is available where the thermal capacity of the CHP unit is 200 kW or less. However only heat generated which is meeting a genuine existing or new demand is eligible. The tool therefore calculates RHI income based on the proportion of heat used on-site and exported, rather than the amount of heat available.
The tool provides an estimate of the capital and installation costs of a hot water CHP unit based on information collected from suppliers and the capacity required. The same grid connection cost as applied to Electricity Generation option is assumed. These costs can be changed by the user if specific estimates have been obtained from equipment suppliers or contractors.
Maintenance costs are assumed to be 5% of capital costs.
CHP: Steam
Packaged CHP units producing steam appear to only be available at sizes larger than would be required by malt distilleries. However a steam CHP unit could be assembled by running the hot exhaust gas from a generator unit through a waste heat boiler. This page of the tool calculates the steam which could be produced under this generation option. Key input cells are:
- Excess Air: In order to calculate the amount of steam that could be generated by this method, the tool first calculates the mass of exhaust gas produced by the generator unit. This requires the “excess air” required by the generator unit to be input. Excess air can be calculated from the air-fuel ratio of an engine, and describes the proportion of air drawn in which is additional to the mass of air required for complete combustion of the fuel. Typical values for the excess air required by an internal combustion engine are between 15 and 25%.
- Temperature of Generator Exhaust/Temperature of Exhaust After Boiler: the amount of energy available for the production of steam is calculated from the drop in temperature of the exhaust gas as it passes through the waste heat boiler. Biogas generation units typically produce exhaust gas at 500°C. As a default, the tool assumes this is reduced to 200°C in the waste heat boiler.
- Steam Requirement Factor: This is the proportion of time in a normal operating week during which steam is required – e.g. the proportion of time during which at least one still is running. It is included to reflect that, although it is assumed in this generation option that the generator is run continuously, steam may not be required all the time by the distillery. The hot exhaust gas produced during times when no steam is required by the distillery is effectively “wasted” – it cannot be used to generate steam (or if it is, that steam would have to be vented). Where the steam requirement factor is low, the heating fuel saving achieved by this generation option is therefore reduced.
- Enthalpy of Steam/Enthalpy of Feed Water: Users who are interested in the mass of steam generated can adjust these inputs to reflect the steam requirements and boiler feed water temperatures at their distillery. As a default, it is assumed steam is required at a pressure of 8 bar. The economic results of the tool are calculated from kWh of steam produced, and so are not affected by changes here.
RHI support is available where the thermal capacity of the waste heat boiler is 200 kW or less. The thermal capacity of a waste heat boiler will be small compared to the thermal capacity of a hot water CHP unit. This is largely because a hot water CHP unit can make use of the lower grade heat from the engine cooling jacket as well as the heat in the exhaust gas.
The tool provides an estimate of the capital and installation costs of a steam CHP unit (generator unit plus waste heat boiler) based on information collected from suppliers and the capacity required. The same grid connection cost as applied to Electricity Generation option is assumed. These costs can be changed by the user if specific estimates have been obtained from equipment suppliers or contractors.
Maintenance costs are assumed to be 5% of capital costs.