Biofuel Production
Research suggested three available technologies for production of biofuel from the draff:
- Biogas using Anaerobic Digestion: organic materials can be broken down by micro-organisms in the absence of oxygen to produce a gas mixture called biogas which consists mainly of methane and carbon dioxide. The process can be achieved at temperatures of around 38° C so has a comparatively low energy requirement, and the process is highly suitable for ‘wet’ biomass. AD is currently widely used in landfill, farm and MSW applications and benefits from specific Feed in Tariffs for energy production from the biogas produced.
- Bioethanol: hydrolysis by heat, acid, or enzymes can release sugars for yeast fermentation to alcohol which can then be distilled to provide bioethanol for fuel use.
- Drying: the draff can be dried to provide solid biomass fuel with a GVC of around 21MJ/kg
The liquid co-product mixture of Pot Ale and Spent Lees could also produce biogas through Anaerobic Digestion. These options were evaluated in the following section to examine their application to Balmenach.
Biofuel Selection
From the mass flowrate of co-product available and expected conversion rates (see Appendix D for figures) for the different processes, a comparison between energy inputs in MWh and outputs in terms of GCV of fuel can be made in Chart 1:
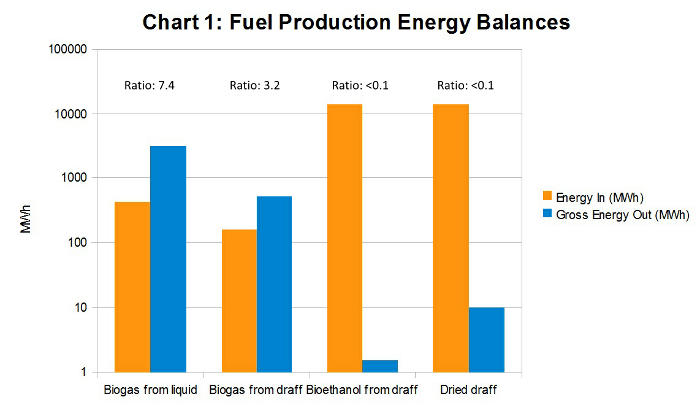
At this stage it was considered to discount bioethanol production on the basis of low yields available with current technology; breaking down lignocellulosic compounds to provide sugars for ethanol production is currently expensive, requiring either large amounts of heat or large volumes of acids or enzymes. Although production of fuel alcohol from distillery waste represents an interesting future opportunity, it was not thought viable at present as most of the available sugar for fermentation has been removed from the barley in the mash tuns.
Drying the draff has a number of drawbacks when compared to AD:
- The energy input required for drying is considerable due to the high moisture content of the solid co-product (70-80%). Steam drying of the co-product would require 3.3kg/kg, making the fuel conversion process energy intensive.
- The energy requirements of the AD plant are mainly low grade heat to maintain operating temperature at 38°C.
- To dry the draff from Balmenach would require an average of 2109.59kg/hr steam at 8bar g over the year, or over 14GWh of heat, possibly requiring an additional steam boiler whereas the low grade heat for the AD plant could be available as a by-product from a CHP unit.
- The conversion of gas and solid biofuel to heat and power can also be compared to show that biogas may be more efficiently converted to higher value energy; the best use of dried solid fuel would be in a biomass boiler to produce heat.
While it may be possible to dry draff economically in a large grain distillery operating continuous distillation where opportunities for process integration exist, this may be unsuitable for small scale distilleries with ‘worm tub’ condensers.
The next decision once Anaerobic Digestion was identified as the most promising currently available option for wet biomass was whether to process both draff and liquid co-products, or to focus only on liquid co-products. Draff and liquid co-product biogas production are shown in Table 2 below:
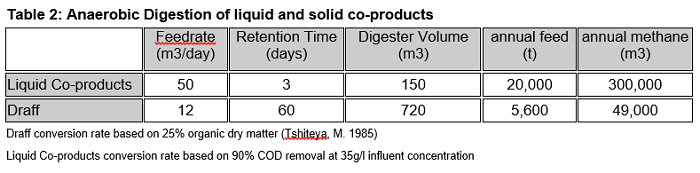
A comparison of the draff and liquid co-product biofuel potential suggests:
- Low degradability of draff in a digester due to lower dissolved solids and lignin requires long retention times up to 60 days.
- Draff requires 5 times greater digester volume (the product of retention time and feedrate); this will have a proportional effect on capital cost.
- Cost of pumping will be higher for draff.
- Liquid co-products will produce around 6 times as much biogas in a lower capital cost AD plant.
Biogas Quality
Interviews with existing technology providers suggest the biogas produced from malt whisky distillery liquid co-products does not contain harmful levels of H2S or other contaminating compounds or moisture, and based on research available, a biogas analysis of 60% methane, 40% CO2 has been assumed for this study.
By-products
The by-product from the AD digester is liquid with COD a tenth of the feedstock (i.e. Around 3.5 g/l). Options for disposal are as fertiliser where demand is available, by sea if agreed with SEPA, or to ground after tertiary treatment such as aerobic or membrane treatment. Best option will depend on the particular site. Balmenach is situated inland, surrounded by agricultural land so it is recommended that the best option would be to sell as fertiliser to local farmers if agreement can be reached.