Appendices
Appendix A: RHI
The biogas boiler may be sized to burn all biogas available, i.e. 359-538kW dependent on expected biogas available, however the recently introduced ‘Renewable Heat Incentive ‘(RHI) is available for boilers burning renewable fuel, but only up to 200kW installed capacity. A de-rated boiler is available at 200kW, and the economic and environmental impact of this option combined with the facility to flare off excess biogas (which would be a harmful greenhouse gas if emitted to atmosphere) was evaluated.
The government has only published a description of the RHI, and not the regulations themselves. However it appears there would be nothing to prevent Balmenach deliberately under-sizing the biogas boiler in order to qualify for the RHI. The remaining biogas could either be used to generate electricity, or a smaller AD system could be installed producing only the volume of biogas required for the boiler. The latter option would reduce capital costs of the whole system, and its financial implications are set out in the “RHI case” in the final row of table __ above. This approach appears to offer financial advantages, particularly if the actual biogas production rate achieved was to be at the lower end of the expected range. However it carries two risks:
- The estimated income available under the RHI case is sensitive to the proportion of the time that steam is required. If this is less than the 75% assumed (see “Methodology and assumptions”, below), the income available under the RHI case would shrink by a similar amount. In contrast, the income generated by the other options in the table is not affected by this percentage.
- The government is considering whether to extend RHI support to anaerobic digester gas boilers of more than 200kW in 2012. If this is done, the income available under the other options in the table would increase.
Appendix B: Technical Considerations
Options A&B: Biogas Boiler
A boiler supplier interviewed suggested that the cost of converting the existing boiler to dual fuel would be approximately £40,000, however this may require the biogas to be scrubbed of CO2 to produce biomethane, and in any case the dual fuel option does not allow simultaneous firing of oil and gas; this suggests a buffer tank would be required sized to contain sufficient gas to meet peak demand. Given that annual biogas production is expected to meet 23% overall thermal demand at best, this was not considered a practical option. Running a biogas boiler in parallel with the existing oil fired boiler would represent a practical solution. The oil fired boiler could be modulated to meet demand as it is currently, with the biogas boiler burning the cheaper fuel meeting a baseload demand. Biogas boilers sized for expected biogas production rates (Option A) and the 200kW RHI limit (see Appendix A), Option B, were investigated.
It was assumed that the total amount of biogas produced under each production rate would be used to raise steam at an efficiency of 80%. This efficiency was based on discussions with biogas boiler suppliers.
It was assumed that steam produced in this way would displace steam generation by the current oil boiler. The volume of oil saved was calculated based on the assumption that this boiler also has an efficiency of 80%: analysis of Balmenach’s boiler log for February 2011 indicates that boiler efficiency varies, but reaches 80% when the boiler is operating well. The oil cost (£0.475/litre) and energy content (11.72 kWh/litre) used in calculations are the same as the figures used in Balmenach’s weekly production report for 2010.
To estimate the size of biogas boiler required, it is assumed that the boiler would be producing steam at full capacity whenever the distillery is operating. This assumption is thought reasonable as the peak steam production rate of the largest boiler above is less than the calculated demand of one still operating at full load, and at any point during operating hours it is rare for none of Balmenach’s six stills to be running. During 2010, the distillery operated round-the-clock 6 days a week for 33 weeks, and 7 days a week for 11 weeks. On this schedule, the distillery operates for 75% of the year.
Boiler cost estimates were for stand-alone containerised boilerhouse installed adjacent to existing boilerhouse, including: Boiler, SS Hot well tank, Blow down Vessel, Water softener, Chemical dosing set, all mechanical interconnecting pipework, all electrical wiring to a distribution board. Ex-Works Budget cost £46,000.00. £15,000.00 budgeted for connection to existing system for pipework, valves, supports and documentation. This gave total installed cost of £61,000 for a de-rated 200kW boiler and £62,500 for 359kW boiler.
Options C&D: Power Generation
As an alternative to the production of steam, the biogas could be used to generate electricity. At this scale, a number of companies supply internal combustion units, packaged either as generators or, with the addition of a heat recovery system, as CHP units. If no suitable use for the heat is available then the generator only option should be investigated as it will entail lower capital costs.
A key question in assessing the economic viability of electricity generation is whether or not surplus electricity can be exported to the grid. Enquiries were made to the District Network Operator; however an answer is not yet available. Two financial cases have therefore been examined. In one export to the grid is possible, in the other it is not.
Option C: Export to grid possible
Where grid export is possible, the generation/CHP unit can be run at constant load and surplus electricity sold back to the grid. Benefits arise in three ways: electricity purchased from the grid is reduced or eliminated; each kWh generated is subsidised through the Government’s Feed in Tariff (FIT) scheme; and surplus electricity can be sold to the grid. The results under each biogas production rate based on Balmenach’s electricity demand and production schedule during 2010 were investigated.
Option D: Export to grid not possible
Excluding holiday periods but not weekends, Balmenach’s baseload electricity demand varies from 20 kW during the warmer months to 30 kW during winter. Peak demand occasionally exceeds 100 kW, and regularly exceeds 80 kW. Under any of the biogas production rates considered, there is enough energy available to supply this demand. However the range between baseload and peak is too great for any of the CHP plants considered in this project to supply: none operate below 50% load. Additionally, large variations in load tend to lead to reduced reliability and increased maintenance costs.
Options E&F: Co-generation of Heat & Power
A number of companies supply packaged biogas CHP units at the scale likely to be required by Balmenach. These tend to use the same internal combustion engine and generator as the equivalent-sized generation units discussed in the previous section. Therefore at a given biogas production rate, the same electricity bill saving, FIT and export income as in the generation only case would be achieved. Heat recovery can provide either low grade heat (i.e. hot water for space heating, or to supply the parasitic heat load of the AD plant) or high grade heat by raising steam. Packaged CHP units producing steam do not appear to be available at this scale. However in theory, a bespoke steam CHP unit could be assembled by routing the exhaust gas from a generator unit through a waste heat boiler.
Option E: Low Grade Heat Recovery
Balmenach currently has little demand for low grade heat. Where it could be used – for example for heating the water used for Mashing, or preheating the liquid in the stills to reduce the mass of steam required for distillation – heat tends to be recycled from the previous run. The AD system itself would require around 10,000 kWh of heat annually in order to maintain its temperature at 38°C, and this could be supplied by the CHP unit. Supplying this load would cost XXX each year at 2010 oil prices if supplied by the current oil-fired boiler.
Option F: High Grade Heat Recovery (Steam Regeneration)
At the scale required by Balmenach, no packaged CHP units producing steam rather than low grade heat were identified. However it may be possible to construct a bespoke system by installing a generation unit and running the hot exhaust gas through a waste heat boiler (a heat exchanger which uses the heat in the exhaust gas to generate steam).
As with the steam boiler option, it is assumed that the output of the waste heat boiler can be used whenever the distillery is operating. As the distillery was operating on a six day per week schedule for part of 2010, and it is assumed that the generator (which acts as the heat source) is shut down during holiday periods, the total amount of steam use which could be offset has been reduced by a factor of 0.89.
The technical information obtained on generation units shows that an exhaust gas temperature of 500°C is typical. The amount of energy that is available for the production of steam depends on the temperature to which the exhaust gases can be cooled. The distillery requires steam at 180°C, and for this analysis a final exhaust gas temperature of 200°C is used.
Although a counter-flow arrangement or economiser could allow more energy to be extracted from the exhaust, further work on the implications of a lower exhaust temperature would be required before this can be recommended. Biogas produced through anaerobic digesters can contain corrosive compounds such as Hydrogen Sulphides. To reduce the risk of these compounds condensing and causing damage, the temperature of the exhaust gas is often maintained above 180°C. Most of the packaged CHP units available do not cool exhaust gas below 180°C, despite the fact they are only heating water to 90°C. None are designed to cool the exhaust gas below 100°C, which would enable the latent heat contained in water vapour to be captured.
In order to predict the energy available to the waste heat boiler, the mass flow rate of exhaust gas was also required. This was calculated from the flow rate of biogas fuel, and a typical value of 20% for the “excess air” drawn in by the engine (excess air is the proportion of air drawn in which is additional to that required for complete combustion). The specific heat capacity at constant pressure of biogas was assumed to be 0.96 kJ/kg.K. It was assumed that 98% of the available heat was transferred to the steam, and the rest lost to the surroundings.
Across the range of biogas production rates considered, the capacity of waste heat boiler required would fall within the 200 kW RHI threshold. Without the RHI, a waste heat boiler is unlikely to be worthwhile in financial terms. Even at a 15 Nm3/tonne SMP, the distillery’s total oil demand is reduced by only 2.5%.
Previously, waste heat boilers have not been available at such small scale, however, this analysis shows that the introduction of the RHI will make waste heat boilers viable at this scale.
Appendix C: Merit Calculations
Following the electrical load:
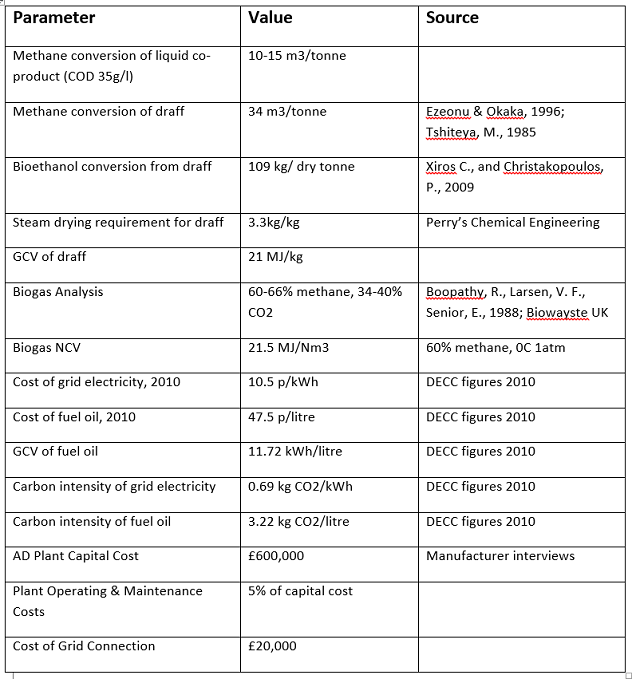
Running at a constant load:
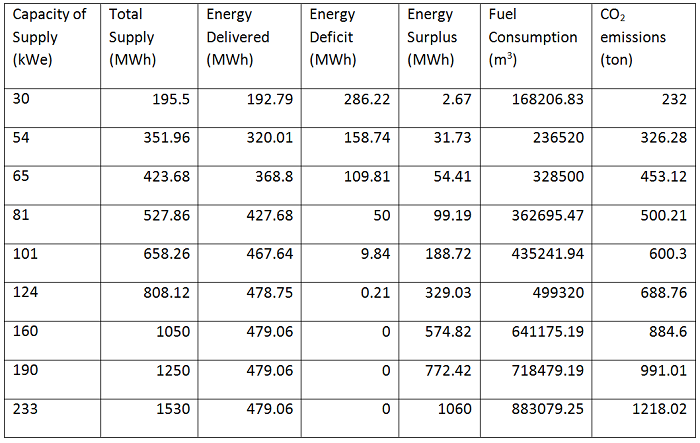
Appendix D: Data & Assumptions
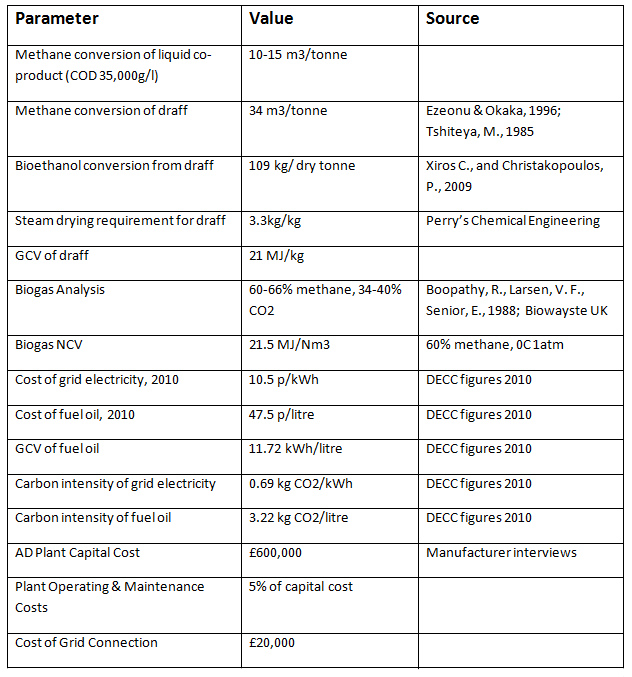