Biogas Production
The Biogas Production page of the tool contains calculations relating to the required Anaerobic Digester system. The five sections are described below.
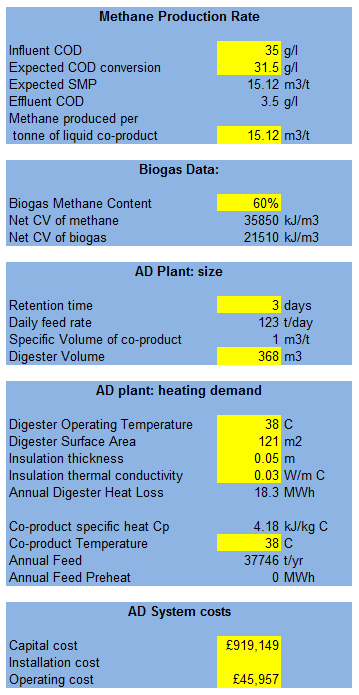
Methane Conversion Rate
The tool applies a conversion rate to the amount of available co-product to calculate the volume of methane which could be produced. The conversion rate is calculated based on the amount the chemical oxygen demand (COD) of the liquid co-product is reduced by during the anaerobic digester process.
- Influent COD: Chemical oxygen demand of the liquid co-product in grams per litre.
- Expected COD Conversion: The amount COD is reduced by during the anaerobic digestion process.
- Expected SMP: Specific methane production rate calculated by the tool.
- Methane produced per tonne of liquid co-product: By default this cell uses the Expected SMP calculated above. The cell is provided so that users can bypass the COD conversion calculation and input a particular methane production rate if they have obtained one by other means.
Biogas Data
Biogas Methane Content: Methane is only one constituent of biogas produced by an anaerobic digester. The other major constituent is carbon dioxide. Information from AD system suppliers indicates a 60% methane content is likely.
The tool calculates the Net Calorific Value of the biogas, based on the Net Calorific Value of methane and the above methane content.
AD Plant: Size
The tool calculates the volume of digester required for the AD system based on the amount of co-product available and the required retention time of the co-product in the digester. Information from AD suppliers suggests a three day retention time is appropriate.
AD plant: Heating Demand
AD systems need to be maintained at a particular operating temperature – usually 38°C. The tool estimates the annual heat loss from a digester (effectively a large tank) at the stated operating temperature. This heat must be replaced, and so an equivalent amount is subtracted from the heat produced by the Biogas boiler and CHP generation options before the economic results are calculated. For the electricity generation option, the cost of supplying this heat from the distillery’s current heating system is added to the annual costs.
To calculate the heat loss, the tool estimates the digester surface area based on the volume calculated earlier. It is assumed that the dominant factor affecting the rate of heat loss is the rate of conduction through the digester’s insulation layer. The heat loss is therefore calculated based on the assumption that the inner surface of the insulation is at the digester operating temperature, and the outer surface is at ambient temperature (it is assumed the digester is located outdoors). The calculation itself is performed on the Climate Data page of the tool, which contains an hourly temperature profile for Oban. This temperature profile could be replaced by the user if greater accuracy is required.
In most anaerobic digester installations, the feed stock needs to be preheated to the system operating temperature before it is added. In the case of a malt distillery, the temperature of the liquid co-products at the end of a distillation run is about 80°C. It therefore seems likely that for many distilleries, preheating would not be necessary. However some distilleries use heat exchangers to transfer the heat remaining in the co-products after distillation to the next batch of liquid entering the stills. In this case, the temperature of the co-products may fall below the AD system operating temperature, and preheating may be required. Users can therefore input a co-product temperature. If this is lower than the operating temperature, the tool calculates the energy required for preheating (“Annual Feed Preheat”).
AD System Costs
The tool produces an estimate of the installed capital cost of the AD system based on the required digester volume calculated earlier. Information on AD system capital costs obtained from suppliers varied considerably, and it is suggested that users consult suppliers for more accurate estimates. Operating costs are assumed to be 5% of capital costs.