Due to the fact that the heat load of the district depends on several different buildings, it wasn’t possible to use the heat demand calculator, offered by our biomass installation feasibility tool, to calculate heat demand of the building. Instead, the values of building heat losses and energy requested were user inputs.
The load profile is shown on the graphic below, with the mean load reaching 4837 kW.

Using the above profile as input for the boiler sizing tool, initially using just one boiler with turn-down ratio of 1:3, the following result was found:

The building process of the district was planned to be implemented in phases. That was one of the reasons to decide for the utilization of two boilers, one installed during the first phase of construction and the second one, smaller, during the final stage. Following the assumption made by the designer, the first boiler would have 4000kW capacity. In the tool this value was input using the option “user input”. The second boiler was calculated automatically. The final result is shown below:
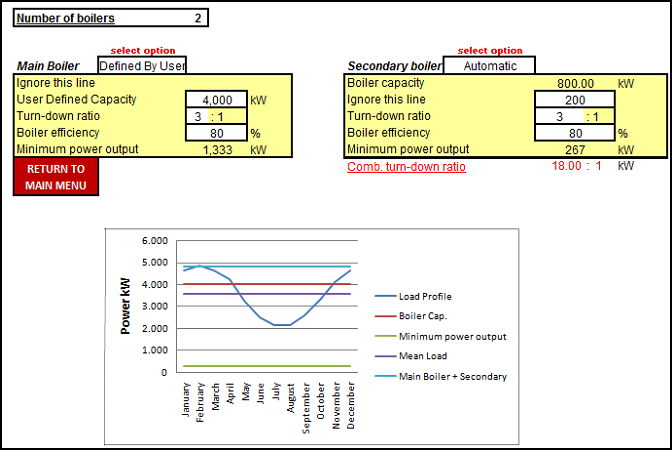
This result matches what was expected. Another interesting observation is the minimum power output of the system. The combination of two boilers turned the initial 3:1 turn-down ratio of the system using one boiler to a turn-down ratio of 18:1.
It was also observed that, for a peak demand of 6800 kW (also estimated from external calculations, not by the tool) a secondary heat source of 2000kW will be required. This solution is different from the one that was actually implemented in the original report. At this point the designer decided to use the secondary source as backup system, switched on to supply the required energy in case of boiler failure. For this reason the secondary source that was originally designed is larger than the one shown in the feasibility tool.
For the thermal buffer sizing the following assumptions were made:
-
The buffer will supply energy for the start-up of the system (in other words, the 4800kW power output was taken into account) and mean hot water for the period of 2 hours.
-
The heating circuit allows a temperature drop of 20 °C
To store the energy for two hours for mean hot water demand (218 kW), the tool indicated the need of 18700 L of water.
For the start-up of two boilers, using M30 fuel, the requested energy is around 2400 kWh, therefore the buffer must supply around 103000 L of water.
After adding the above values, the result showed that the total amount of water to be stored is 121560 L. Comparing with the report used as reference for the study, a difference of 1000L in the size of the suggested buffer by the report and the one calculated by the tool is observed. This difference is smaller than 1%.
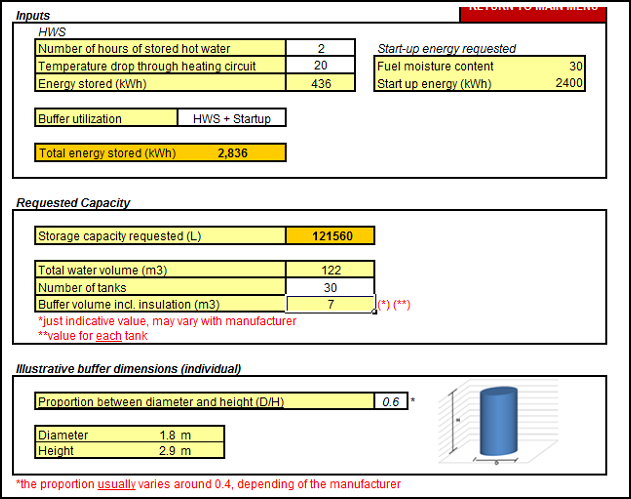
The report does not offer detailed information about the monthly energy consumption of the building, making it impossible to compare results in this area with the tool. Using the energy consumption calculated by the tool, total annual consumption of 27 000 000 kWh is expected, compared to 23 000 000 kWh defined by the report.
It is expected , from the results presented by the tool, that the fuel consumption will follow what is represented on the graphic below:

Two woodchip silos - 14m long by 3m wide by 3m deep were designed. Using this information with the tool and selecting a fuel with 30% of moisture content, it can be observed that this will be enough to store 93 tonnes of softwood.
If the delivered fuel cost is 1.3 pence per kWh, filling the whole silo would cost around 4,212 BGP, which would be done around 62 times per annum, knowing that the annual consumption is 23,000,000 kWh. Also, the estimated storage capacity, in days, for each month is shown below:
Back to top
|