The Technology
Currently the technologies for extracting power from marine currents are underdeveloped with no single device dominating the market. In terms of basic principals, a lot can be drawn from the experience of wind turbines, as the fluid dynamic behaviour and laws of physics around the devices is fairly similar; yet the operating conditions differ quite considerably. Most notably water is considerably denser than air, therefore the size of the turbine required to extract energy from the water can be smaller than a wind turbine, which can have significant cost benefits. However, the increased density does mean that the materials used for marine applications need to be stronger and more durable in order to withstand the large thrust loadings generated in the subsea environment. The harsh marine environment also presents several other design considerations when selecting the materials for marine current devices. Sea water is a saline solution, therefore the materials used need to be corrosion resistant. Bio-fouling from marine life can affect performance of a device and reduce its structural integrity; therefore measures to address these factors need to be considered when selecting the correct materials to reduce its potential impact.
Environmental considerations also need to be taken into account when designing, installing and operating marine current devices, in terms of their potential impact on marine life and marine eco-systems. These include the potential impact of the materials used, the operation of the device and any disruption caused during their installation and maintenance.
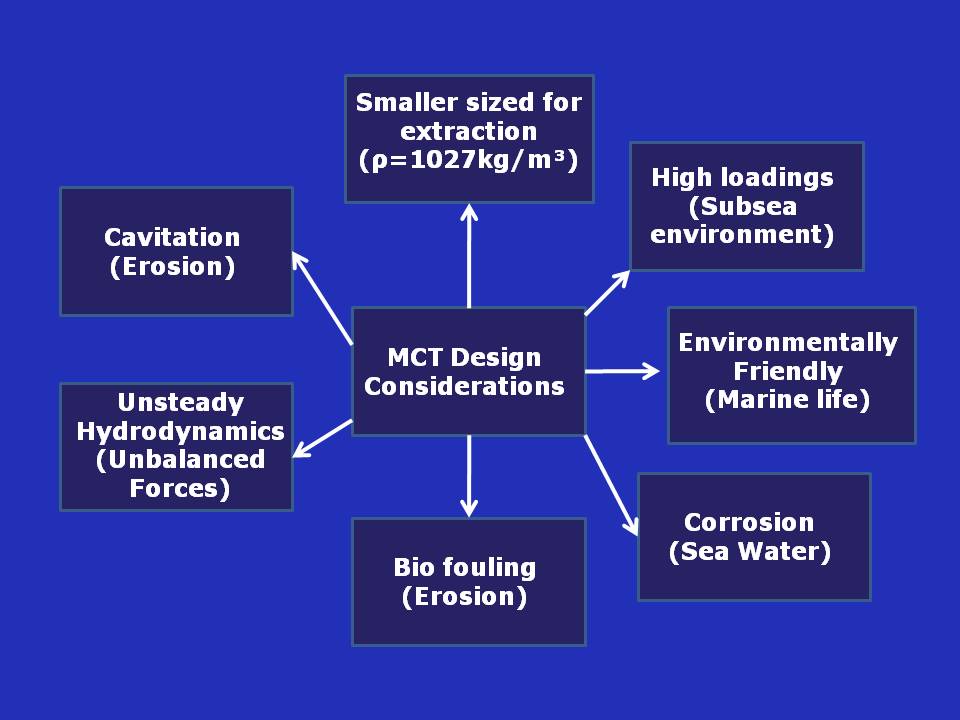
Other factors which must be considered in the design and conceptual stages include: cavitation, velocity shear, turbulence and the presence of surface waves. Cavitation is a hydrodynamic effect most commonly observed on ship propellers which is caused when the static pressure of a liquid falls below that of its saturated vapour pressure. As a result of this process, small bubbles are formed on the hydrofoil surface which eventually collapse and implode. This effect can be detrimental for rotational marine devices, causing vibration and structural damage over time with the potential to induce unbalanced load distributions, conceivably reducing their overall lifespan. Velocity shear, turbulence within the flow and surface wave effects will also contribute towards unbalancing the loading on marine devices and need to be well understood, well predicted and factored in during the design and conceptual stages.
For most of the designs proposed so far, the horizontal-axis wind turbine is being used as the standard model. Design and performance codes based on wind turbines are being utilised and their methodology applied to marine applications, with most based on Blade Element Momentum Theory (BEM). In this case the devices are rotational comprising of a hub and blade configuration with some form of supporting/mooring structure. Pitch regulation is commonly applied to the blades of these devices in order to stop the turbines gently when at full flow. Fixed pitch devices would require a brake to stop them, which would need to be very powerful at full flow. If the brake failed, the turbines could not be stopped. These devices are also usually designed so that they can generate power in both tidal directions. There are currently several rotational marine current devices under development within and out with the UK.
Other designs under development include oscillating hydrofoils, vertical-axis turbines and open ducted and contra-rotating rotors. The structures used to moor these devices to the seabed or fix their position in the flow field also vary greatly.
There appears to be no clear route as to what will be the most advantageous and cost effective arrangement, which has opened up a whole new and exciting market for design and innovation within this particular engineering discipline.
References:
www.marineturbines.com