Maximise Revenue
It has clearly been identified that blade surface degradation will present a significant issue to tidal current turbine operators and can have considerable economic implications. A tidal current turbine will need to be designed with marine growth, cavitation, and erosion in mind. These are all factors which can degrade the surface characteristics of tidal current turbine blades.
Marine Growth (biofouling, biofilm, fouling)
When a vessel such as a ship sits in a harbour it will only take one day for microorganisms to attach to its bottom. Within a week these organisms create a slimy substance in which growth can occur. After two weeks barnacle larvae and other marine life will be able to enter this environment and grow. There exist multiple options for boat owners to protect their vessels from fouling.
As part of this project the group has identified multiple coatings that can be considered by designers and developers. Selection of coatings will depend on many variables. One of the most important factors is the predicted maintenance schedule for the tidal energy farm. For performance testing of various antifouling coatings this group recommends reading ASTM 4939-89(2007).
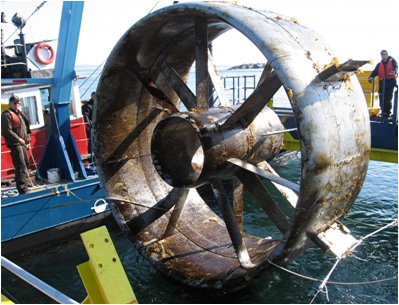
Cavitation
Cavitation is a hydrodynamic phenomenon where vapour bubbles are generated and collapse on a surface when the fluid is subjected to a drop in pressure. In the case of a boat hull, hydrofoil, propeller or marine turbine blade this phenomenon will occur when speeds near or surpass 15m/s (30knots). In the propeller industry high strength metals are used to survive the effects of cavitation. In some cases, propellers have been replaced due to holes being worn straight through them. The entire marine turbine will not experience this speed; however blades tips can easily reach these speeds if the designer is not careful. To test blade materials and coatings for cavitation a designer is recommended to use the ASTM G32 process.
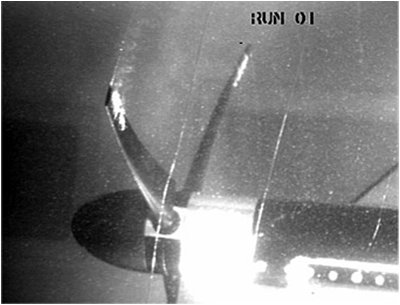
Erosion
If a proper coating is selected erosion should be of little concern. Some coatings are designed to withstand high volume traffic on factory floors by fork trucks, containers and employees. However, there are various ASTM abrasion tests that can be performed by the designer to ensure that the selected product meets expectations. This is highly recommended as usage of ships in sea miles can be hard to compare with the typical operation of a tidal current turbine.
Knowledge of erosion resistance is also necessary for developers when planning blade cleaning. If the coating is unable to withstand the removal of antifouling by brush or high pressure water jet then it is unlikely to be selected. To test blade materials for erosion a designer is recommended to use the ASTM G73 process. To test coatings please see ASTM D4938-89(2007).