Power Calculations
This section presents the equations later used to calculate the power savings of a Flettner rotor on the chosen ship and route. Equations and their terms are presented, the only results of calculations that are included here are those for the power consumption of the rotor, the rest of the results are shown on the energy savings page.
To calculate the percentage power savings available on the chosen route from a Flettner Rotor it is essential to first calculate the power required to overcome the chosen ship’s resistance, the power consumed by spinning the rotor, and the usable power. It is important to also state which power uses will not be considered in the calculation. Primarily these include, power lost from bearing friction, power used to accelerate the boat up to the cruising speed of 13.3 knots, operation around ports, power used to accelerate/decelerate the rotor to an optimal rpm, and the additional power needed to overcome drag from the rudder – which is being used to counteract the yaw moment induced by the rotor. These considerations were disregarded due to the timescale and limitations of the project, but are noted to be important considerations in a truly realistic estimation of power savings. The equation for the power saving for each section of each journey is shown below.
Where P_s represents power saved, P_g the useful power generated, and P_c the power consumed by the rotor. To represent as a percentage saving this can be divided by the power required to overcome ship resistance, P_b.
P_b can be calculated by multiplying the resistive force on the ship due to the water, F_b, by the speed it is travelling at, U_b (Lele & Rao, 2017), although this value is also calculated from the MAXSURF study.
The useable power generated, P_g, from the Flettner rotor can be calculated using the same equation except with the forward thrust force, F_T, as explained in the background theory section. Finding F_T will give additional challenges which are addressed in the ‘finding the optimal spin ratio’ section.
The power required to spin the Flettner rotor has been simplified to the power required to overcome the frictional forces from the air, as stated above the bearing friction and acceleration power consumptions are not included. To calculate the power required to overcome air friction additional parameters are required. The rotational Reynolds number, Re_Ф, is required for rotating cylinders as explained in detail in (Childs, 2011) and the skin friction coefficient C_f, which is approximated using the 1/7 power law (CFD Online, 2016) is used to obtain the frictional force F_f from the air. Equations for these parameters are shown below, where ρ is density of air, ω is rotational velocity in rad/s, r is radius of the rotor, μ is dynamic viscosity of air, U_tan is tangential velocity of the cylinder, and A_w is wetted area (in this case the circumference of the cylinder multiplied by the height).
Using an air density of 1.225kg/m^3, a radius of 2.5m, dynamic viscosity of 1.81e-5kg/m.s, and a calculated wetted area of 471.239m^2 gives the following power curve for rotational speeds of 2-180rpm, which is the operational range of a 30x5m Flettner Rotor as specified by Norsepower (Norsepower, 2018).
The R^2 value of 1 shows the trendline used to produce the equation on the graph is a perfect fit to the data. The equation shown on the graph can now be used in future calculations to obtain power consumed by the rotor for different rotational speeds.
References
CFD Online, 2016. Skin Friction Coefficient. [Online]
Available at:
[Accessed 29 March 2019].
Childs, P. R., 2011. Rotating Flow. Burlington: Elsevier.
Lele, A. & Rao, K. V. S., 2017. Net Power Generated by Flettner Rotor for Different Values of Wind Speed and Ship Speed. Kollam, IEEE.
Norsepower, 2018. Norsepower. [Online]
Available at:
[Accessed 5 April 2019].
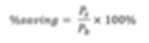
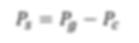
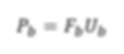
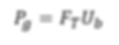

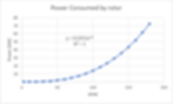