This project will apply the methodology,
outlined previously, to the construction village at
Laing O’Rourke’s Xscape site. The construction village consists of 26 modular contractor’s
cabin linked together over 2 storeys and 9 jackleg cabins used
by subcontractors.
Contractor’s accommodation is constructed to current Building
Regulations regarding their specification of insulation.
It is however, notable that the subcontractor’s cabins are of
an older model with poor insulation envelope.
The construction village consists of offices, meeting rooms,
toilets, canteen, kitchen and a drying room for both contractors
and subcontractors.
Back to Top
Our objectives are to demonstrate significant improvements
for chosen areas of the Xscape site by applying the energy
efficiency measures that were identified in the previous
section. By applying the first step of our methodology, which is
concerned with demand side management, to the Xscape site we
will achieve improvements in the following areas:
1.
Energy Demand
2.
Thermal Comfort
3.
Environmental Impact
Further outcomes from the Xscape study will be:
1.
Investment costs
2.
Payback Periods
Back to Top
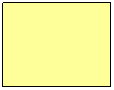
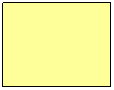
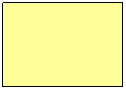
The first step of this study is to identify areas with a high
energy demand. In these areas we will then apply a number of
selected energy efficiency measures. In order to identify significant areas within the Xscape
site, the accommodation layout, the power installed in every
area, the quantity of a certain area as well as the periods of
energy usage have been studied, considering the information
obtained on the Demand Analysis of the Project Web Site.
§
Xscape
contractor’s accommodation layout
§
Power
installed in every area
§
Periods
of energy usage
Then, by studying the complete construction village we have
identified the following target areas:
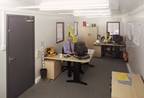
Offices
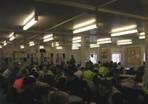
Canteen
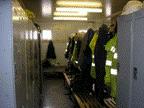
Drying
Room
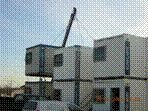
Subcontractor’s
Cabins
It shall be mentioned that the Xscape site contains 13
contractor’s offices, one contractor’s canteen and drying room
and 9 subcontractor’s cabins.
In the next step the appropriate energy efficiency measures
are identified which shall be implemented in the selected areas. These measures have previously been summarised in our demand
side study. The figure below shows the energy efficiency measures applied
to each area.
Offices
• High frequency ballasts
• Daylight control system
• 1.5 kW heater with automatic control |
Canteen
• High frequency ballasts
• Occupancy sensor for lights
• 1.5 kW heater with automatic control
• Ventilator (428m3/hr) with heat recovery
and CO2 sensor |
Drying Room
• High frequency ballasts
• Occupancy sensor for lights
• 1.5 kW heater with automatic control
• Ventilator with 157m3/hr with heat recovery
and humidity sensor |
Sub-contractor’s Cabins
• Improved insulation
• 36W T5 fluorescent lights
• Occupancy sensor for lights
• 1.5 kW heater with automatic control |
The last step is to carry out an analysis for these areas
using the selected measures in comparison to their current
situation.
Back to Top
In this case study we conduct an analysis for the chosen
areas with the help of ESP-r. This is done by assessing our proposed situation in
comparison with the current situation on the construction site. The proposed situation is based on implementing previously
identified energy efficiency measures in the selected areas.
This case study is based on the actual room sizes occurring in the
Xscape construction village and also takes into account the
surrounding area of the various rooms as well as the working
behaviour of all employees. Working hours are assumed to be 11 hours per day
for 5 days a week and 52 weeks per year.
The case study can be accessed via a link in the Demand Side
part of the Project Web site.
Back to Top
In the
following all results arrived from the case study are tabular or
graphical listed for:
·
The 13
contractor’s offices
·
The
contractor’s canteen
·
The
contractor’s drying room
·
The 9
subcontractor’s cabins
The main
results are listed in the table below.
Accommodation |
Annual Energy Savings
£ |
Capital Investment
£ |
Payback
Period
yrs |
Avoided
CO2 Emission kg/yr |
Offices
|
|
|
|
|
Lighting |
221 |
2600 |
11.8 |
|
Heating |
1001 |
1690 |
1.7 |
|
Total |
1222 |
4290 |
3.5 |
11,258 |
|
|
|
|
|
Canteen
|
|
|
|
|
Lighting |
206 |
1050 |
5.1 |
|
Heating |
113 |
520 |
4.6
A |
|
Ventilation |
- |
615 |
|
|
Total |
241 |
2185 |
9.0 |
2,247 |
|
|
|
|
|
Drying room
|
|
|
|
|
Lighting |
87 |
410 |
5 |
|
Heating |
1489 |
650 |
0.4 |
|
Ventilation |
- |
320 |
- |
|
Total |
1342 |
1380 |
1.0 |
12,395 |
|
|
|
|
|
Subcontractor’s Cabins
|
|
|
|
|
Lighting |
648 |
1800 |
2.8 |
|
Heating |
2160 |
2340 |
1.1
B |
|
Total |
2808 |
4140 |
1.5
/ 8.8
C |
26,109 |
Note:
A
shorter payback period in case of unventilated space
B
no consideration of extra hire costs for well insulated cabin
C
considering an additional yearly hire charge of £260 for a well
insulated cabin
Furthermore,
all results are shown in the following graphs.
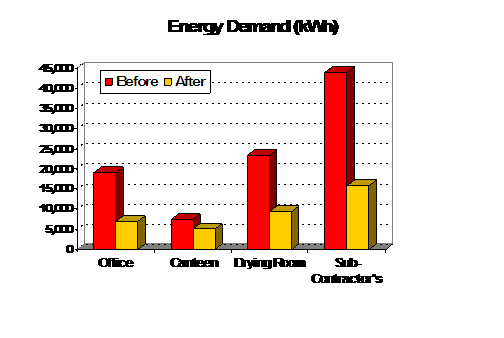

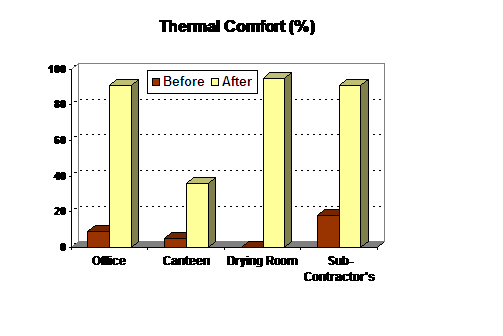
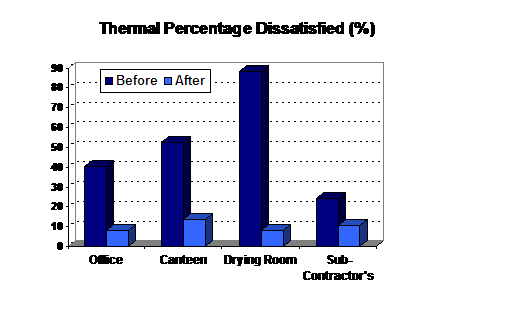


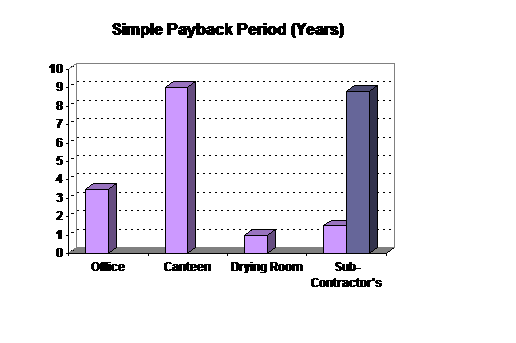

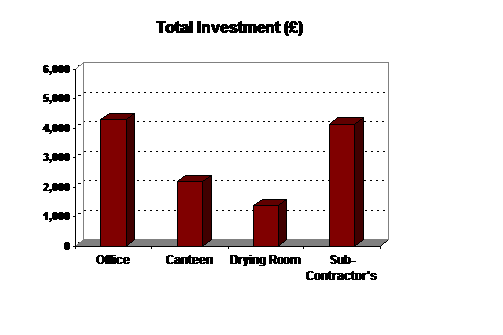


Notes:
1 Thermal comfort and thermal percentage dissatisfied are
stated for a typical winter day
2 Thermal comfort: percentage of working hours with a dry
resultant temperature 20°C – 22°C
3 There are two values on the Simple Payback Period for the
Sub-contractor's. The longer payback was calculated taking into account the extra hiring charges of good insulated
cabins while the shorter payback just assumed the company
purchasing from new.
Back to Top
In conclusion the
following goals have been achieved:
-
Reduction of
annual energy demand
-
Reduction of
annual energy cost
-
Reduction of
annual carbon emissions
-
Improvement
of thermal comfort
-
Decreased
number of dissatisfied employees
It has been demonstrated that the application of energy efficiency
measures can lead, in the Xscape construction village, to
energy savings between 32% and 64% depending on the target area.
This report indicates that, because of their high
percentage of energy savings but relatively low payback periods, the
contractor’s offices and the drying room are primary targets for
implementing selected energy efficient lighting, heating and
ventilation equipment. In case of the drying room the application of
ventilators with heat recovery and humidity sensors will
additionally provide an effective environment for clothes to dry and
therefore solve a main problem faced on every construction site.
Changing the
subcontractor’s cabin on the Xscape site by hiring well insulated
cabins and applying selected heating and lighting measures requires
a high initial investment. However, improving subcontractor’s
accommodation will lead to a significant reduction in annual carbon
emissions which will contribute towards achieving national targets
and thus help to lead towards sustainable development.
Despite savings of energy and carbon emissions, by applying our
methodology in the Xscape construction village the environmental
comfort of all areas investigated will be enormously improved. This
will lead in to a working environment where employees are able to
work effectively due to the improved level of comfort.