Other Pages within Case Study:
Within this page:
|
Case Study
Analysis of the Holsworthy biogas plant, Devon
|
The UK's first centralised biogas plant is at Holsworthy in Devon, England. Because some of the published data from Holsworthy's construction and operation were used during the creation of our model, it is not ethical to use Holsworthy as an independent validation of our model accuracy. However, since our model pulls together so many pieces of information and provides useful insights, it is interesting to analyse the Holsworthy plant using our calculator.
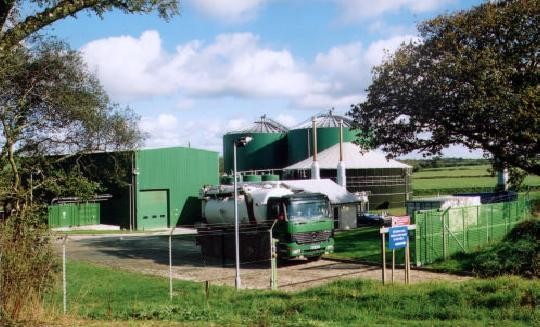
Data concerning the construction and operation of the Holsworthy plant has been gleaned from presentations from the plant designers Farmatic [http://www.bathandwest.co.uk/journal.shtml#bioseminar], plant website
[http://www.holsworthy-biogas.co.uk/]
and personal contact with the plant manager. The Holsworthy feed stream consists of approximately:-
- Manure from 3750 dairy cows, spread out over 25 farms, within an 8km radius.
- Litter from 200000 hens and chickens.
- Miscellaneous commercial food waste, 40 tonnes/day, which incurs gate fees.
Other key information available about the plant includes:-
- Capital cost was £7.7 million, although £500,000 improvements were recently added to comply with the new EU regulations.
- Capital grants were obtained for 50% of the plant cost.
- Electricity is sold at a price of £0.058/kWh under an NFFO contract. Currently there is no revenue from exportable CHP.
- Operating expenses are estimated at £450,000 per annum.
- Each year, the plant expected to receive revenue of £800,000 from electricity sales.
- Each year, the plant expected to receive revenue of £200,000-£300,000 from gate fees, but this has since risen by "five to ten times".
- The plant processes about 400 tonnes per day.
- There are 2 digesters and 3 pasteurisers.
- Biogas production is about 6 million m3/annum.
- Biogas yield is about approximately 40m3 per tonne of feed.
- Electricity production is approximately 14.4 million kWh per year.
- No money changes hands between the plant and the farmers for either manure feed, or for digestate products. The plant has to pay for feed collection, but farmers collect the digestate (free of charge) with their own transport.
We also assumed:-
- A discount rate of 8% per annum.
A gate fee of £45 per tonne. This applies to food waste only (not to manures). Evidence we have seen in several sources quotes gate fees in the range of £35 to £70 per tonne. This is notably higher than current landfill prices (£13-14 per tonne), but is being driven up by the new landfill directive.
- We assumed that waste feed streams and digestate are transported by lorries with 20 tonne capacities, £40/hour costs, speed=25km/h, pumping speed=50 tonnes/hour, 8 hours a day on 5 days of the week available for deliveries, lorries based 1km from the plant, 1 hour a day driver lunch break, and 3.27 km/litre diesel consumption.
- A 20 year plant lifetime.
Archived inputs and outputs from our model of the Holsworthy plant can be viewed at
Holsworthy demographics and Holsworthy results.
- Our model predicts that we must add a small amount, 15 tonnes/day, of water. This is to maintain a dry solids content less than 12%. The commercial food waste, hen & chicken litter feed streams are quite dry. Some water is required to dilute the feed stream so that it can be processed. The overall feed stream is about 400 tonnes/day, of which 400-15=385 tonnes/day is manure and food.
- The C:N ratio of the mixed waste stream is about 15.
- Our model predicts a biogas yield of approximately 40m3/tonne of feed, and 5.6 million m3/annum total production. These estimates compare well with the actual/published figures of 40m3/tonne and 6 million m3/annum.
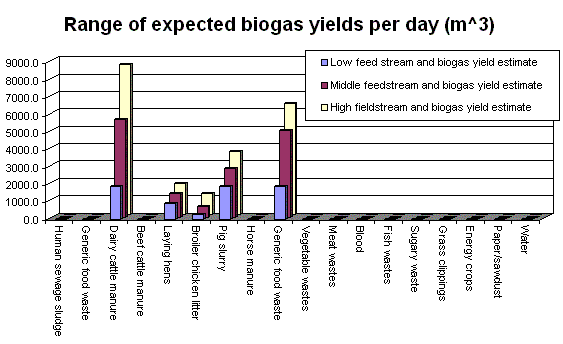
- Our model predicts an expected (MIDDLE) annual electrical export of 11 million kWh, with a range of 4 million kWh (LOW estimate) to 18 million kWh (HIGH estimate). The published figure from Holsworthy is 14 million kWh.
- Our model predicts an expected revenue from electricity sales of £630,000, while the published figure is £800,000.The energy balance below displays, that overall, the plant is an efficient producer of electricity and heat. Process and transport energy requirements are far outweighed by the energy produced.
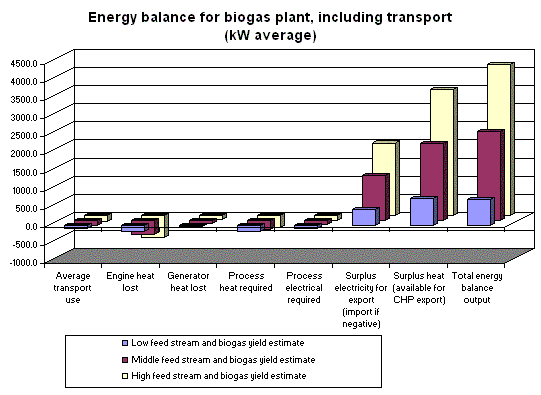
- Based on the 40 tonne/day commercial food waste stream, gate fees estimated by our model are £660,000 per annum. Holsworthy published figures were £200,000-£300,000, but have since risen by "five to ten times".
- Our model predicts that the capital cost of the Holsworthy plant would be between £6.3 and £9.6 million, with an expected value of £8 million. This matches well with the published cost of £7.7-£8.2 million.
- Our model predicts an annual running cost of about £550,000 compared to the published value of £450,000.
- Overall, our model does not predict the Holdworthy plant to be profitable, even taking into account the 50% capital grant that was received. A financial balance of Net Present Value (NPV) over a 20-year plant lifetime is shown below.
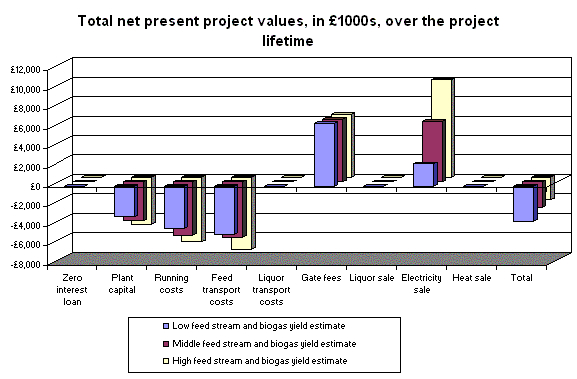
Although our model predicts that the plant is not profitable, it is worth commenting on why this is so, and what factors could be adjusted to justify the plant commercially.
- The transport costs associated with the collection of cattle manure and pig slurry are relatively high, as these manures have a relatively high moisture content and correspondingly low biogas yield per tonne. On average, on each delivery day (monday-friday), 27 20-tonne lorry deliveries of feed must be made to the plant each day. Our model predicts that for this plant, 7 20-tonne lorries are required to maintain this delivery rate from the surrounding distribution of feed pickup points. This compares with the Valorga case where our model predicts only 9 20-tonne feed deliveries per delivery day, achievable by only 2 20-tonne lorries.
- No revenue is being generated from heat sales. More revenue could be generated by successfully exporting heat at a sensible price, say £0.003/kWh.
- Zero revenue is being generated from digestate sales. In reality, the plant is run as a cooperative by the farmers. The digestate has a fertiliser value for the farmers as the Nitrogen, Phosphorus and Potassium content of the digestate liquor and fibre makes it a valuable replacement for chemical fertilisers. As such, although the digestate is not sold for a fee, it displaces fertiliser cost for the farmers, who have a stake in the plant.
Adjusting the heat sale price from 0 to £0.003/kWh and factoring in a digestate sale value of £2 per tonne (at roughly 6% dry solids content, and where the farmers still pay for digestate transport from the plant to their farms), results in a plant that has a net present value of £550,000 and an IRR (internal rate of return) of 9.9%.
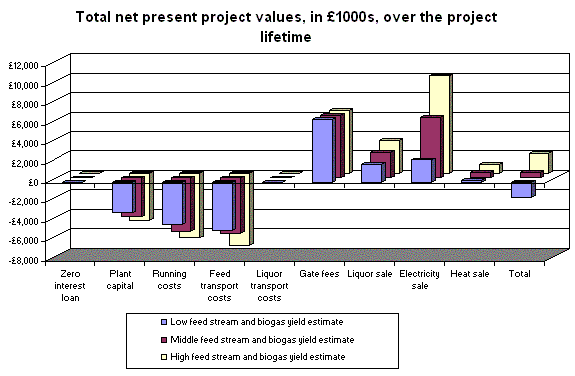
Holsworthy represents a plant which can just just profitable, with some grant funding and by being run on a cooperative basis. The farmers must put some money into the plant, either directly against running costs or by paying nominal amounts for the digestate that they receive. This revenue from the farmers is justified by the them receiving the processed digestate liqour and fibre in place of the raw manure that they donated. Although the processed liquor and fibre has a higher fertiliser and compost value than the original manure, a fair relative cost per tonne is still relatively small since, at 6% dry solids on average, the digestate is bulky and heavy.
Profitability could be increased if larger markets could be found for the digestate as fertiliser, but these markets do not yet exist in the UK. Any digestate sale strategy will also be limited by the relatively large cost of transporting the digestate to any buyer. Drying the digestate from 6% dry solids to make it easier to transport is an option, but an expensive and risky implementation.
|